Industrial Furnace and Oven Portfolio
References from clients should be the foundation of confidence behind your choices in service partners
IFS is a leader in the field of industrial thermal process design, construction, and maintenance. Below is just a partial list of projects stretching back to 2011 (miscellaneous upgrades, add-on units, confidential clients, and our most current work may not be included). As these references demonstrate, our work involves a wide range of scale and scope. If you wish to learn more, or arrange a reference or visit, please contact us.
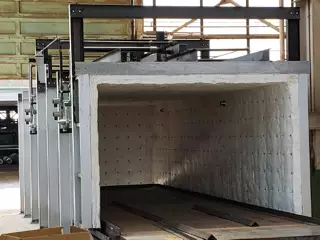
Provided with only an empty steel shell, IFS designed and installed a new excess air bleed-off burner system, complete with new burners and NFPA compliant fuel train. This project project included fabrication of a new exhaust flue and insulation of all walls, door, and flue. The new design/modification provided the customer with a reliable car-bottom batch furnace with a uniformity capable of +/- 5° F.
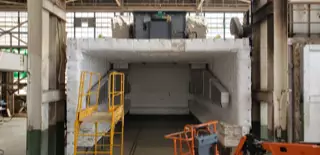
Provided with only 3 steel walls after demo, IFS modified an old car bottom furnace into a new tempering furnace. The project featured fabrication and installation of a new roof structure and hot box, complete with new burner assembly and NFPA compliant fuel train. Also included in the project was the installation of two new 25,000 ACFM fans and associated ducting, as well as all fiber insulation. Once again, the IFS new design/ modification supplied a temperature uniformity of +/- 5° F.
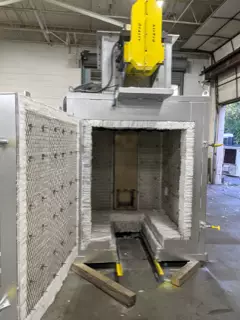
IFS designed and fabricated complete turnkey new electric convection oven. With an operating temp of 250° F - 1200° F and a load capacity of 3,000 lbs., this new oven provided the customer with enhanced performance and reliability. As a result of its satisfaction with the project, the customer has purchased an additional identical oven from IFS for a separate operational site.
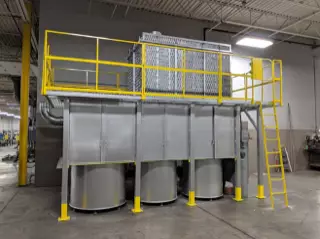
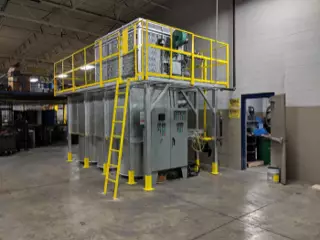
IFS engineered, fabricated, and installed a fully functional platform and ventilation system, capable of handling 1000 cfm of process waste air. IFS provided all the necessary superstructure, a hot box afterburner complete with a new burner and NFPA compliant fuel train, 3 new melting pots with containment enclosures, all associated ducting for proper ventilation, and a new electrical control cabinet.
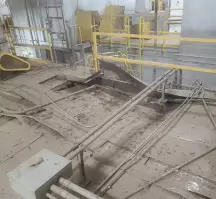
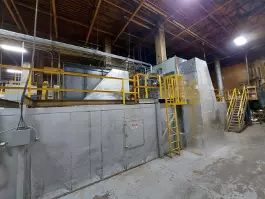
IFS was commissioned for an emergency repair to a 120 ft. long belt oven that had suffered an accidental explosion. The damage was wide ranging and included the hot box and the majority of the side walls and roof panels. IFS did not just carry out repairs, it determined the cause of the explosion and engineered solutions that would prevent a future re-occurrence. This critical re-construction project was complete - start to finish - in just 2 months' time.